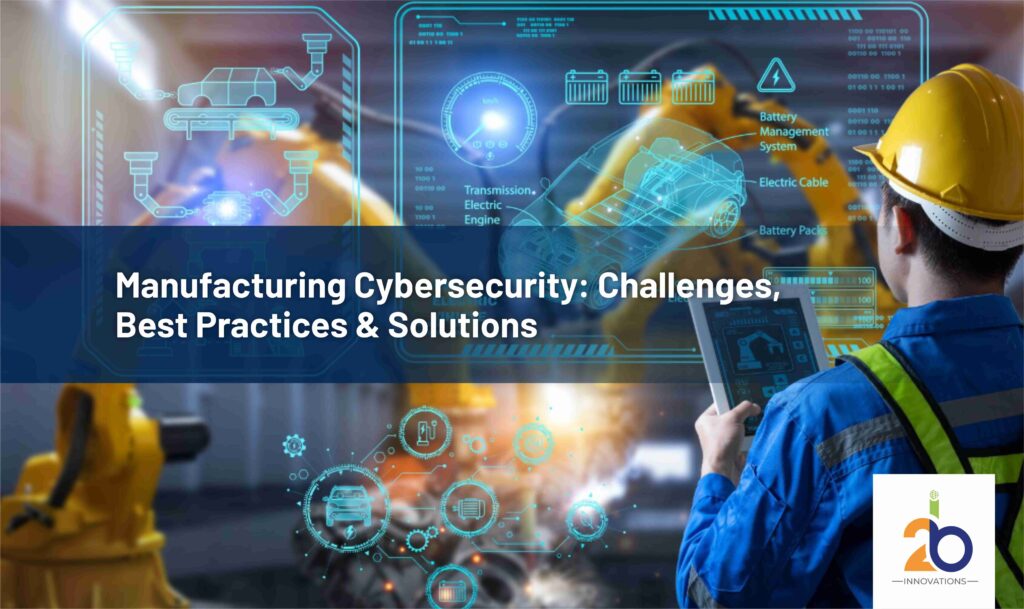
The manufacturing industry is a broad sector that has wrapped up many lines of work, including the automotive, aerospace and defense, chemical, food and beverage, pharmaceutical, and medical device industries. The manufacturing industry has brought a big revolution to the nation and society by contributing to economic growth, technological advancement, job creation, and the provision of essential goods and services. Amongst this era of growth and success, the plagues that have let down the productivity of manufacturers are the cyber attacks and threats that expose the weaknesses inherent to the increasing (and otherwise beneficial) interconnectivity of the information technology (IT) and operational technology (OT) environments that hold up their operations.
Now, manufacturers’ comprehensive cybersecurity strategy is needed to keep going with this connectivity and prevent their exposure to cyber risks from worsening. The key insights and factors to look for while setting up the cybersecurity strategies are as follows:
What is Manufacturing Cybersecurity?
Are you aware of what factors have witnessed the rise of the Manufacturing industry? The credit goes to technological advancements like
automation and integrating IoT devices and other cyber-physical systems (CPS) throughout processing, production, packaging, and other essential operations.
Such upgrades have led the way in the growth and connectivity of Manufacturing industries, resulting in the increased demand for manufacturing cybersecurity, which is more important than ever. An efficient
cybersecurity strategy aims to safeguard the CPS on which production availability, integrity, and safety depend.
Achieving that goal requires manufacturers to embrace an approach beyond traditional IT security solutions and principles. As ransomware infections continue to halt assembly lines, rogue insiders remotely alter configurations to compromise production, and other types of attacks that exploit security weaknesses in CPS persist, manufacturers must adopt security principles that are purpose-built for CPS. Before we jump into what they are, we must examine the cybersecurity challenges those principles will address.
What Are Manufacturing Cybersecurity Challenges?
1. Legacy systems are the norm
Industrial technology (OT) assets that makers use today were put in place decades ago before it was common for OT environments to be connected to the internet. When these assets weren’t connected, they weren’t exposed to cyber risks and didn’t need cybersecurity controls. Because makers’ profits have always depended on uptime, software patches for many of these decades-old assets have only been applied sometimes. After all, patching takes time, and time off slows down work, and work that gets done leads to income. As a result, even the most successful makers’ OT environments still have a lot of assets that aren’t protected and legacy systems that have been left unpatched and full of holes that cybercriminals have already shown they can and want to use as weapons.
2. Proprietary protocols and delicate processes prevail:
Older OT assets and more current CPS types often use protocols that can’t be used with standard IT security tools. Many of these tools also use a lot more resources and traffic than most CPS could handle, so they can only be put in place without risking messing up the important but fragile physical processes they serve. Standard inventory and asset management systems also need help with compatibility. This is a big reason why it’s so hard for manufacturers across all industries to find and protect the CPS that makes up their OT environment.
3. Remote access is a must
Most manufacturers use remote access to let employees and outsiders keep the CPS running in their OT environments. 99% of the time, traditional IT solutions like VPNs and jump servers are used for this. However, these solutions are often hazardous and ineffective because they need to consider OT’s specific operating and security needs. Amanjeet Singh, Managing Director of 2b Innovations, says, “People with direct access to OT networks are a top threat vector for targeted attacks on OT systems.”OT engineers often shared executive access in the past because they needed to get to the process immediately. Those tasks are even harder to do now that many of them are logging into OT settings from home. As long as manufacturers rely on OT remote access, they must be aware that attackers will probably keep looking for ways to use the standard solutions that make it possible.
4. Ransomware is increasingly common and damaging:
In the past few years, the manufacturing industry has witnessed a drastic change with the increase in ransomware attacks. These attacks have disrupted assembly lines and taken advantage of weak spots in the CPS that are necessary for the availability, integrity, and safety of automotive production. Because of the interconnected nature of most manufacturing supply chains, a ransomware assault on one link in the chain can affect not only other manufacturers but also distributors, retailers, and consumers. Ransomware attacks can occur anytime, and when talking about its effects, it puts your data and intellectual property at risk. They may harm your company’s reputation and cause problems with safety implications. Attacking an industrial control system (ICS) or a safety-critical process in the OT setting could impact employee safety and cause physical harm.
Key Principles for Securing OT Environments in Manufacturing
If you want to fix the problems listed above in manufacturers’ OT environments and keep your company safe from new and changing cyber threats, you should follow these three key rules that were designed to keep CPS safe:
1. Gain visibility into all CPS in your OT environment
For industrial cybersecurity to work, you must have a full list of all the OT, IoT, IIoT, BMS, and other CPS assets supporting your OT system in every manufacturing plant. Analyzing this kind of insight is a difficult and important thing that security and risk leaders must do now. Because of this, 2b Innovations provides many adaptable discovery methods that can be mixed and matched to provide full access in the best way for your organization.
2. Integrate your existing tech stack and workflow from IT to OT
We already discussed how only some CPSs work with standard IT solutions. Those solutions still have a place in OT. With 2b Innovations, you can safely find risk blindspots without risking your operations because it doesn’t add to your already large tech stack. By bringing existing tools and workflows from IT to OT, this approach will help manufacturers take control of their risk environment and get a better view of things across teams that usually work in separate areas.
3. Extend your security governance from IT to OT
Most OT environments in the manufacturing sector have different governance or critical cybersecurity controls than their IT peers. Again, this is because many OT environments have old systems built with utility and operational reliability in mind rather than security since they were initially meant to be disconnected from the internet. 2b Innovations closes this hole by bringing your IT controls to OT. This unifies your security policy and guides all your use cases towards cyber and operational resilience.
Manufacturing is a significant sector in the global economy. It creates jobs, advances technology, builds infrastructure, facilitates foreign trade, and more. Industrial Internet of Things (IIoT), automation, and advanced analytics make production smarter and more efficient. This is an example of how digital change can help. However, using digital technologies has also made it easier for hackers to attack and given manufacturing companies more problems to solve.
Businesses need to learn how to deal with these dangers, follow best practices for cybersecurity, and use a CPS protection platform, such as Claroty, to create a strong cybersecurity posture and support all use cases as they progress in their security journey.